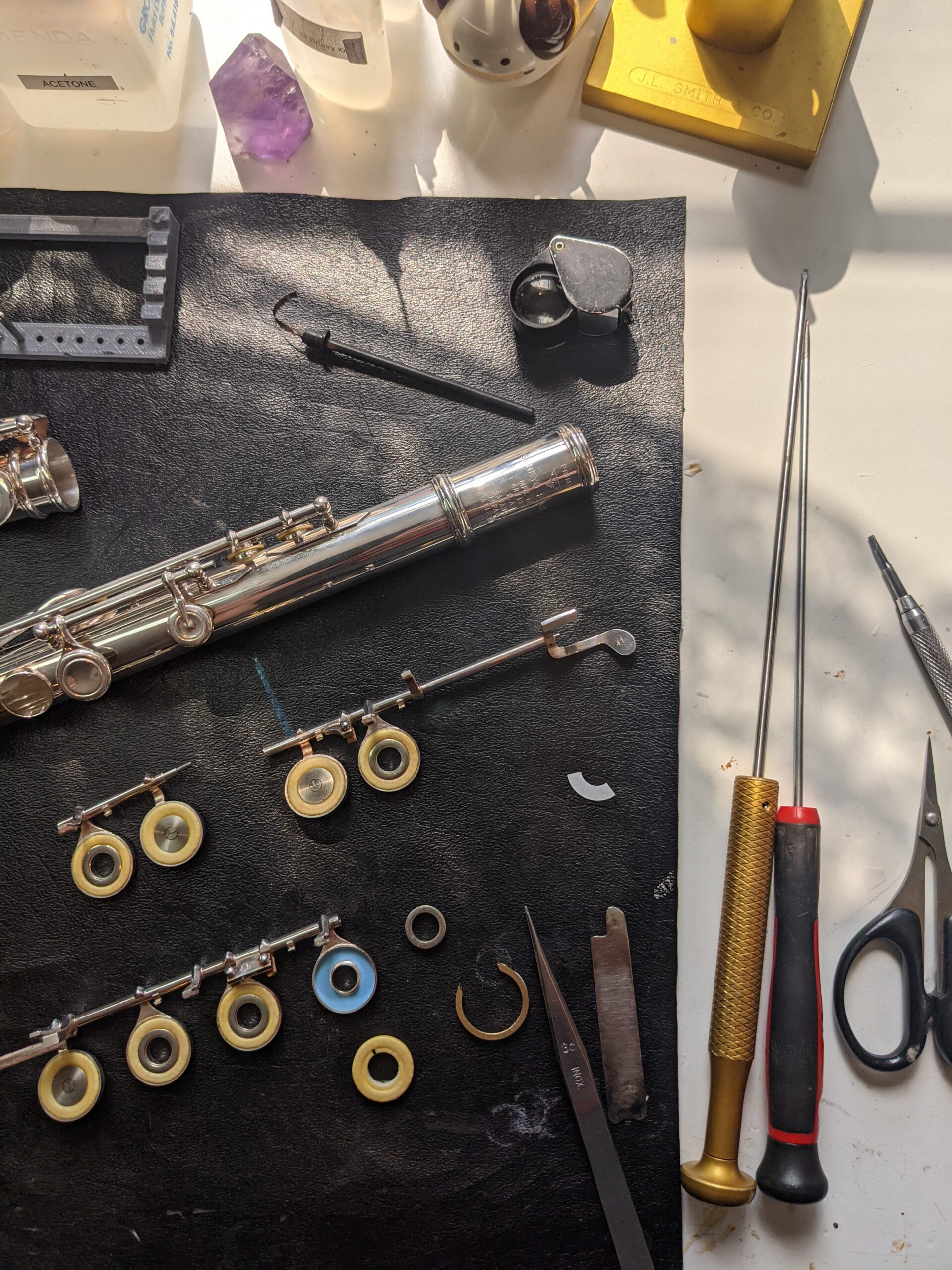
By Rachael Simon
As a professional flute repair specialist, one of the most common questions I receive from flutists is, “What kind of pads should I get?”. I love getting asked this question, because pads are probably one of my favorite things to talk about. It’s for good reason–there are few components that are as crucial to the sound and performance of a flute as the pads that are in it. If the headjoint is the voice of the flute, the pads are the heart.
Whenever I hear “What kind of pads should I get?”, I actually hear two questions: “What kind of pads are best for me?” and “What kind of pads are best for my flute?” These are the questions that both you and your repair technician should work to answer before a flute is overhauled or re-padded. The answer is often a balance between what you would like, and what your flute would like. These are also important considerations when selecting a new or new-to-you instrument to buy. To find the answers to these questions, let’s first look at how pads interact with the flute.
Flute anatomy
Flutes are designed by the manufacturer to work with a specific pad type. Not only is the body and mechanism constructed with a certain pad in mind, but the headjoint is also designed and cut to work acoustically with the intended pad as well. The primary aspects of flute design that pertain to the pads are the tone holes, key cups, mechanism, and headjoint.
Tone holes
A soldered tone hole is a separate piece of material that is soldered onto the body tube. A drawn tone hole is extruded, or “drawn” from the tube. When it comes to flute padding, the quality and flatness of a tone hole matter more than whether it’s drawn or soldered. The only disadvantage of drawn tone holes from a padding standpoint is that the amount of leveling that can be done is limited, which may or may not be a problem depending on the quality of the tone hole and the type of pad being used.


Key cups
Flute key cups are typically made one of two ways: Punched (also called stamped), or machined. A punched cup will be concave and have multiple contours where the pad seats, whereas a machined cup will be flat. The cup design is an important indicator of what type of pad will be the best match for the instrument.


Flute pads are installed in the key cups with shims, a washer and screw, or an open hole bushing, and sometimes a stabilizer depending on the situation. Most shims are made out of either paper or Mylar, a type of plastic. Shimming is a massive and mind-bending topic that I will resist the temptation to delve into here, but shims are essentially used to both level the pad and to correct leaks caused by an imperfection in the tone hole surface, the pad cup, or the pad itself. The flatter the pad, cup, and tonehole are, the more stable the pad is, and the easier the flute is to adjust and maintain.



Mechanism
The precision of the pads directly pertains to the precision in the mechanism. Can an imprecise mechanism be made more precise? Generally, yes, but just how precise it can be is ultimately limited to the original standard of manufacture. A firmer pad requires a mechanism that is functioning within very tight tolerances, and tone holes that are flat or nearly flat. For instruments that are built to looser tolerances and with unlevel tone holes, a softer and more forgiving pad is appropriate.

Headjoint
The headjoint will often influence the pad choice by the manufacturer, and vice-versa. How is the headjoint related to the pads, when it’s not even touching them? Well, in a way, it is–it’s touching the pads acoustically. A hand-cut headjoint does have its own unique characteristics that will be evident no matter what type of pads are in the flute, but it absolutely will sound different depending on what pads you pair with it. When the headjoint maker is cutting the headjoint at the factory, they will use a flute body produced by that manufacturer and with the current spec pads that the company offers on that model. The headjoint maker play-tests the headjoint continuously throughout the headjoint cutting process, playing after each small change is made until they are happy with the sound. In short, the headjoint was cut with the acoustics of those very pads as part of the equation. That doesn’t mean that the headjoint won’t sound any good if you switched the type of pads in that flute, but it does mean that it will sound a bit different.

As you can see, pads are related to practically everything about the flute. Now that we have an understanding of how pads relate to the body, keys, and headjoint, let’s talk about the pads themselves.
Most flute pad designs follow a similar concept. There will be a core pad material, a “skin” that is wrapped around the core pad material, and a backing of some kind. It’s the materials used for these components that make for the big differences between pad types, both in acoustics and in suitability for the individual instrument and player.
You will find that the strengths of each pad type are also often their weakness as well. As with everything else about the flute, pads are all about balance, and each flute/player combination will have their own unique requirements.
All pad types have their own acoustic character. The description of this character is subjective, as well as dependent on the flute headjoint design. With this disclaimer, I will be including my own general opinions about the acoustics of each pad. This is how I describe each pad type to my customers, to help with their decision-making process. Each player (and each technician) will experience a flute slightly differently.
Common pad types:
- Woven felt
Woven felt pads are the essential, traditional flute pad. The vast majority of flutes produced in the 20th century were designed and padded with woven felt pads, and there are still many flutes being produced with these pads in the present day.
Woven felt is fairly soft, which makes this pad type more forgiving of imperfections in build quality, as well as forgiving of leaks that can occur due to changes in humidity and temperature. These pads are usually the pad of choice for vintage and antique instruments, due to their adaptability to tone hole and key cup irregularities. They are also preferred for student flutes for the same reason. On the other end of the spectrum, woven felt pads are also suitable for highly accurate, modern handmade instruments. Some modern handmade flutemakers believe that this is still the superior pad type, and use them in their finest instruments. A quality woven felt pad is incredibly versatile!
Due to the nature of the material, woven felt is more reactive to changes in humidity and temperature than other pad types. That being said, their forgiving nature makes it easier for the player to compensate for such changes. For small changes, the player often doesn’t notice the tiny bit of extra effort that pressing down these soft pads requires. The danger is that over time, the leaks will become gradually worse. Since the change happens little by little, the player gradually presses harder and harder, often without realizing it. This extra finger pressure over a long period of time can lead to compromised technique, hand injuries, shortened pad life, and mechanism damage. If these pads are set up very thoroughly and well, seasonal changes in pad coverage can be minimized, but the capacity for change will always be there due to the organic nature of the material. Therefore, it is important that woven felt pads are adjusted every 12-18 months, even if the flute still sounds fine to you.
Acoustics: I describe the acoustic characteristic of the woven felt pad as rich, warm, and colorful. This pad will also tend to have a darker sound, depending on the headjoint that they are paired with. Nearly all of our favorite flute soloists from the 20th century had these pads in their flute, for what that’s worth!



- Pressed felt
Pressed felt pads have become increasingly popular over the last few decades, and are now the standard factory pad for many intermediate flute models. Some manufacturers that produce flutes with felt pads have replaced woven felt pads in their instruments with pressed felt. They are also a common choice for felt pad overhauls on professional flutes. These pads are much more dense and hard than woven felt, and therefore are less reactive to changes in humidity and temperature. This practically eliminates one of the major drawbacks of traditional woven felt pads.
However, the advantage of pressed felt does come with a couple of additional considerations. Firstly, because pressed felt pads are so much harder than their softer woven felt counterparts, they are not nearly as accommodating of imperfections of any kind. Therefore, when something does change, it is going to be much more difficult for the player to compensate. Secondly, the more unforgiving nature of this material means that more perfection in the flute is required for them to be set up well. That means that the mechanism, tone holes, and key cups need to be more precise for these pads to be feasible to install to a high standard. Not every flute is physically capable of being brought to this standard, so the additional stability that pressed felt pads can provide is limited to the flutes that can accommodate them.
Acoustics: Pressed felt has a brighter and more powerful sound than woven felt. It will also usually sound more crisp. Despite these differences, I do find that this pad type maintains the colorful sound of felt. These pads sound fantastic when installed accurately on an appropriate flute.



- Straubinger
Straubinger pads have become a household name in the flute world for good reason. I do not feel that I am overstating things when I say that Straubinger pads revolutionized the handmade flute industry. Straubinger pads were introduced in the 1990’s, and it did not take long for many high-end flute manufacturers to switch from felt pads to Straubinger.
So what makes these pads so special, and so different? Well, nearly everything! The only material that Straubinger pads have in common with felt pads is the traditional double layer “skin”. Aside from the skin, every other component is synthetic. Whereas a felt pad has a relatively thick felt disc, the cushion material of a Straubinger pad is a very thin disc of synthetic microsuede. Instead of a thin cardboard backing, there is a plastic (delrin) shell that holds the pad material. This all translates to a pad that is very hard, and very flat. Since it is virtually impossible to create a felt pad that is perfectly flat, Straubinger pads solved this problem by having a precision-machined shell for a very thin pad that is extremely consistent and accurate. The more flat and accurate the pad is, the higher the potential for the flute to be sealing well.
Additionally, since these pads are almost entirely made of synthetic materials, they are not reactive to changes in humidity and temperature. Another classic flute padding problem that Straubinger addressed was the irregularity of the key cups themselves. A precision-machined flat stabilizer is put inside the cup, and the pad and shims are seated on this flat surface rather than directly on the key cup.
These pads are amazing, right? Why don’t they put these in every flute? Well, the reason is that they are too perfect. All of the characteristics that make them so stable and accurate are the things that require a highly accurate flute body and mechanism. Not every instrument is designed to meet these rigorous standards–in fact, the majority are not. For this reason, this pad type is typically seen only on high-end handmade flutes. The firmness of the pads leaves little forgiveness for any imperfections. Imagine a felt pad being like a mattress, and a Straubinger pad being like a yoga mat- the yoga mat will be far less forgiving of imperfections in the surface that it is placed on.
Straubinger has always been very clear about these requirements, so much so that they host Straubinger Certification classes every year for qualified technicians. This intensive course provides technicians with the knowledge and training they need in order to correctly service flutes with Straubinger pads. The flute needs to be mechanically set up to work precisely and with tight tolerances, and the tone holes need to be level. If the flute in question is not built this way from the factory, then it needs to be professionally overhauled and made to be this way. Many handmade flutes are great candidates for this procedure.
However, intermediate or worn-out professional flutes may not be able to ever achieve the mechanical precision and tone hole flatness that these pads require. This is something that your repair person will advise you on, should you ever be interested in converting your flute to Straubinger pads. If your flute came with Straubinger pads from the factory, then it is already designed to accept them. It is very important to see a Straubinger-certified technician for service if your instrument has these pads.
Acoustics: Straubinger pads are highly resonant and vibrant. They also provide a clean and crisp response that is difficult for any felt pad to beat. Projection and power are as effortless as delicacy and softness. It is easy to see why this is the preferred pad for so many professionals and amateurs alike!



- Pisoni S2
This will be a short section, because the Pisoni S2 is extremely similar in construction and sound characteristics compared to Straubinger pads. This pad was released by Pisoni following the end of the Straubinger patent on their pads. That being said, it is not an exact copy. The design of the delrin shell is slightly different, and instead of a double layer of skin, there is a single layer of a very durable, high quality laminated pad skin. These small differences are more for the technician to consider than the player–acoustically, they are essentially the same pad, and I have never once noticed a difference in sound between a flute padded with Straubinger and then with S2 (or vice-versa). The same Straubinger installation principles apply to S2, so I still recommend having a Straubinger-certified or otherwise highly trained repair person install S2 pads in your flute. The S2 is a world-class professional flute pad in its own right!



- JS Gold
JS Gold pads are a unique offering on the market. These are the firmest of all the common flute pad choices, and are therefore suitable only for the most precise, level, and rigid flute setups. If the tone holes cannot be made absolutely perfectly flat, and if the mechanism is not built to the tightest of tolerances, these pads are not a good match for the flute.
The JS gold pad is one of the very few completely synthetic pads available. There is a synthetic film in place of a conventional pad skin, which is embedded with gold. The cushion is a thin synthetic foam disc. The backing and shell materials are composed of a combination of delrin and aluminum.
Acoustics: The sound of JS Gold pads is often described as dark, clear, and focused. The sound of every pad depends on a high quality installation, but with JS Gold Pads, this becomes even more important due to their firm and unforgiving design.



- Straubinger Phoenix
Straubinger Phoenix pads are a unique and relatively new offering for flutists. These pads were developed by Straubinger to be suitable for flutes that were not designed to accommodate the original Straubinger pads: a bridge between the forgiving nature of classic woven felt and the stability of a machined synthetic pad. The Phoenix pad does share some characteristics with the original–it has a delrin backing, a microsuede cushion, and a double layer of traditional pad skin. However, where it differs is crucial. Instead of a single cushion disc, the cushion material is a double layer, with the top layer being wrapped around the edge of the pad. This makes the pad very soft, in stark contrast to the classic Straubinger pad. The wrapped top layer of microsuede also is not perfectly flat. Though the Phoenix pad is not flat, the maker’s intention is that the softness of the pads allows for enough give to compensate for the irregularities. These pads are not designed to function the same way as the originals, where perfection is required. Instead, these pads thrive in imperfect environments, allowing for an upgrade to instruments that are otherwise not accurately made enough for classic Straubinger pads.
Acoustics: Because of the softness of the Phoenix pad, it is not typically as crisp or clean sounding as the original Straubiinger pad. However, it still has the vibrancy and resonance, as well as some additional richness and warmth, thanks to the extra layer of cushion material.


- Manufacturer-specific pads
Several makers choose to produce their own pads for their instruments. There are some ingenious and beautiful pads out there that are specifically designed by manufacturers for their flutes alone. With all of the pad knowledge you now have, you can imagine how critical these specialized pads are for the acoustics and mechanical performance of the flutes they are paired with. Therefore, it is a good idea to check with the manufacturer to see if your flute has brand-specific pads, and if a factory-trained technician is recommended for service.
Though most good technicians can look at any pad setup and gather the basic principles of the design, there are often small but important details that only the manufacturer or manufacturer-trained technicians will be aware of. These pads will also often require specialized techniques. The moral of the story is: know your pads, and know your technician!
With this information, you now have a window into what makes your flute sound and function the way that it does, and some insight on its design. This article is by no means an exhaustive list of all the knowledge that a repair person uses when recommending a pad type for your flute, but hopefully it will give you a clearer idea of the factors being considered. This is also not a finite list of all of the available pad types. However, you will likely find that these are the pad types most commonly offered by technicians and discussed among players.
The most important point that I can leave you with is to develop a relationship with a technician who understands both you and your flute, and has the knowledge and experience to serve you both. You and your instrument need to be considered together–you are a team, after all! The pads in your flute play an enormous role in your voice and your playing experience. I hope this article leaves you feeling more enlightened about the way flute pads work, and provides some clarity on the different pads available.
Rachael Simon
Website | Facebook | Instagram
Rachael Simon is a highly trusted flute repair specialist based out of Eastern Pennsylvania. She is Straubinger Certified, Muramatsu Certified, and her shop is the official Burkart Repair Center East, serving the entire East Coast and New England. Rachael is known for her careful attention to detail, mechanical expertise, and relentless pursuit of perfection. She has repaired and maintained flutes for top professionals around the world, including instruments for Haynes, Powell, Burkart, Miyazawa, and Yamaha artists. Rachael is also an accomplished flute repair instructor, and has had numerous students and apprentices go on to become top flute finishers and repair technicians. Rachael regularly presents on repair topics for flute events, repair shops, and private instructors.
Rachael holds a Bachelor of Flute Performance degree from Miami University, where she studied with Randolph Bowman, Principal Flute of the Cincinnati Symphony Orchestra, and Dr. Sandra Seefeld. During her studies, Rachael’s love for the flute manifested into a love for the flute as a beautiful machine, and decided to devote her efforts to learning flute repair. In 2011, Rachael went on to join Burkart-Phelan, Inc, where she worked for 6 years. In addition to working as a finisher and repair technician, Rachael studied advanced repair techniques with Lillian Burkart and Jim Phelan. Her capabilities extend to precision machining, wood instrument crack repair, plating, and beyond. Rachael was also in charge of quality control operations for the highly-regarded Resona product line during her tenure. She additionally maintained a private repair shop that serviced all makes and models, earning acclaim from regional professionals and instructors. In 2016, Rachael continued her pursuit of fine flute repair by joining JL Smith and Co. as a flute and piccolo repair specialist. Her padding techniques and 9th mechanical ability earned her a reputation for bringing flutes to their highest performance potential in both sound and feel.
Rachael has operated her own independent flute repair specialty shop in Doylestown, PA since 2018. She brings her dedication to the craft, finely-honed precision, and deep love for the flute and piccolo to every job. Her passion is using her knowledge and skills to make each instrument a seamless joy to play for every flutist, whether professional, student, or amateur.

[acadp_carousel_slider]
Rachael–this is an amazing article and I learned so much. You have a knack for taking a complex subject and making it easily understandable. Kudos to you for making this information accessible for all flutists!
Πολύ ωραίο και χρήσιμο άρθρο για εμάς,για τους φλαουτιστες.Εκτος που παίζουμε το όργανο,πρέπει και να γνωρίζουμε και τις λεπτομέρειες του οργάνου και για την κατασκευή… Με κατανοητό τρόπο μας εξηγήσατε αυτές τις λεπτομέρειες. Συγχαρητήρια ??
Πολύ ωραίο και ενδιαφέρον άρθρο. Ετκος από το να παίξουμε το φλάουτο,πρέπει και να γνωρίζουμε τις λεπτομέρειες του οργάνου,για την κατασκευή,για τύπους μαξιλαριών κ.τ λ…Το εξηγησαντε με κατανοητό τρόπο.
Συγχαρητήρια για αυτό το άρθρο ??
I realize I am late to the game, but I have a question. My flute technician explained the pad differences very much like this article. However, despite my flute being able to accommodate them, he did not recommend Straubinger or JS pads for me because of the venues I play. I primarily play jazz, folk, etc in bars, camps and restaurants. He felt that the Straubinger pads were much more likely to be unseated due to a bump in these venues and would not be able to stand up to that type of environment. Any thoughts?
Could you tell me what kind of pads are originally on a Geminhardt M2 flute?
I have two, one in the A series, the other in the B series.
Thank you ?
This is such an excellent article, providing the basics for us as players to understand well what is going on under the keys, and how to plan an overhaul and selecting pads optimally. Thank you so much!
One question: how would yo place the Star LP pads made by Pisoni? I have a feel that they are close to the Straubinger Phoenix design, but what do you professional techs think/know?
Thank you for such an excellent, thorough article! As an instrument repair tech generally frustrated by flute repairs, I’ve found myself wanting to learn more, particularly about the best material choices and what I may or may not be fighting against. So glad I came across this in my research. Now I’ve got to go do some testing. Thank you!
A brilliant example of the world of pads iam a novice to the flute world and started at at late age but it’s a wonderful instrument to learn I’ve also started replacing my own pads as being technically able to accomplish many different tasks I have managed a full strip down on my own Jupiter flute with good success it took quite a bite of time but very satisfying,informative information like provided is a goldmine for me and I will continue to read avidly this site’s wonderful knowledge of the flute. Many thanks for sharing your expertise and wisdom.
COST TO REPLACE PADS ON “DECENT ” FLUTE SOME SAY ,IT’S CHEAPER TO SIMPLY , BUY NW FLUTE ???MARTIN